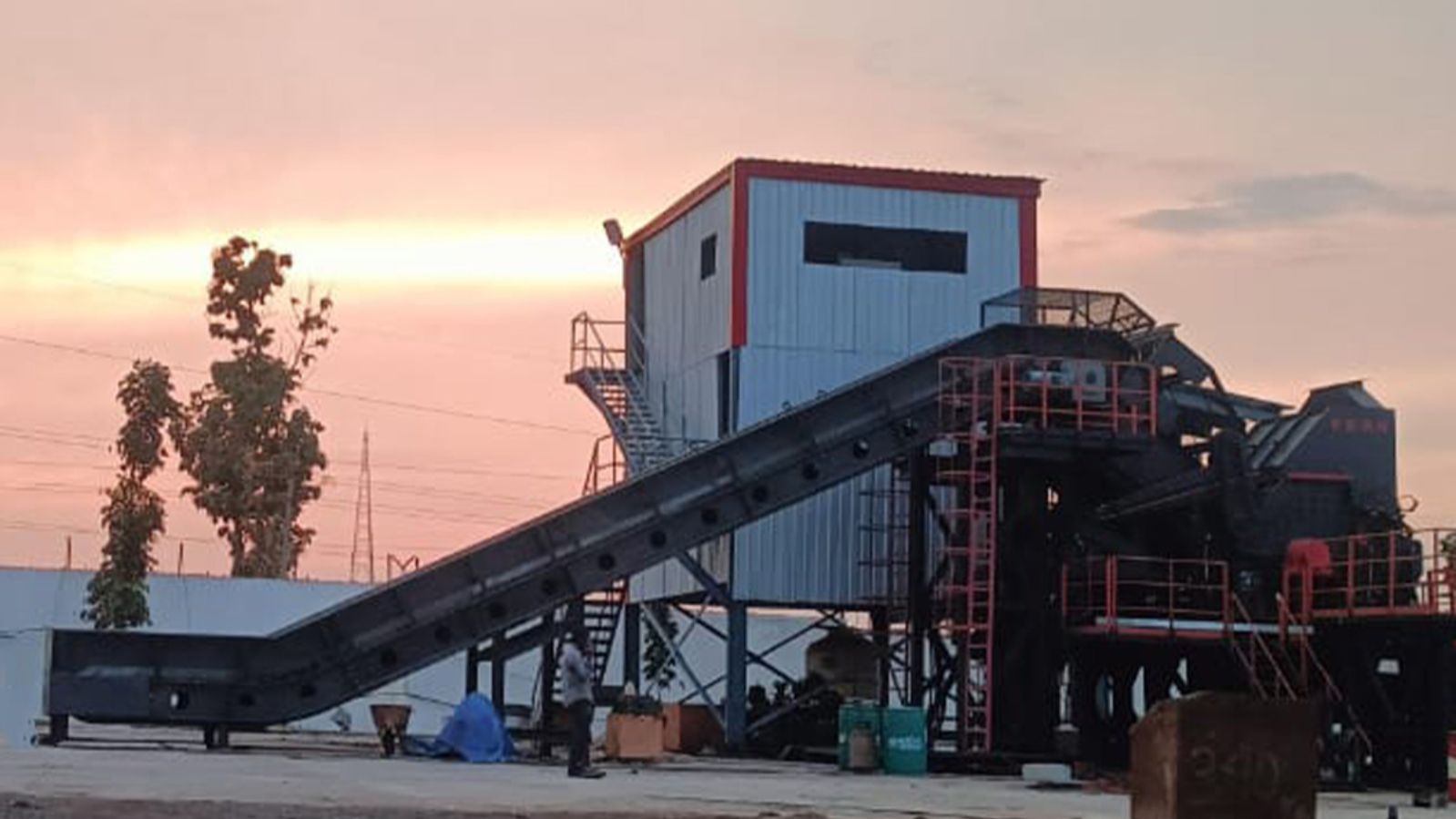
Selecting the right type of metal crusher machine for your specific shredding application is crucial to ensuring efficient and effective metal shredding operations. Here are some steps to help you choose the right type of shredder:
- Understand Your Shredding Requirements:
Start by understanding your specific shredding requirements. Consider factors such as:
- The type of metal materials you need to shred (e.g., ferrous or non-ferrous metals)
- The size and shape of the materials (For example, elv dismantling or tyre shredding)
- The desired output sizes
- The desired shredding capacity (i.e., throughput)
Understanding your shredding requirements will help you determine the type of shredder that best fits your needs.
- Consider Material Characteristics:
The characteristics of the metal materials you need to shred are important in selecting the right shredder. Factors such as material hardness, thickness, and density can impact the type of shredder that is most suitable. For example, materials that are hard or thick may require a more robust and powerful shredder, while softer materials may be effectively shredded by a less powerful shredder. Intelligent Edge offers different types of robust shredders with different intensities based on the unique requirements of the client.
- Evaluate Shredder Types:
There are several different types of shredders available, each with its own strengths and weaknesses. Some common types of metal shredders include:
- Single-shaft shredders: These shredders have one rotating shaft with blades that cut and shred the material. They are suitable for a wide range of metal materials and are generally used for moderate to heavy-duty shredding applications.
- Dual-shaft shredders: These shredders have two rotating shafts with blades that work in tandem to shred the material. They are typically used for very light metal scrap shredding applications like shredding very thin sheets, cans, steel barrels, etc., usually material that is less than 2 mm thick.
- Quad-shaft shredders: These shredders have four rotating shafts with blades that provide even more cutting and shredding capabilities. They are suitable for heavy-duty shredding applications and can handle a wide range of metal materials.
- Hammer mills: These are the most commonly used in the world. These shredders use hammers to break up the material, making them suitable for softer materials. They are typically used for lighter-duty to medium-duty shredding applications. These shredders provide the highest quality shredded scrap, free from impurities and having a higher density.
- Granulators: These shredders use rotating knives to cut the material into smaller pieces, making them suitable for smaller metal materials and for applications that require precise control over the output size.
- Consider Additional Features:
Additional features that may be important for your shredding application, such as the availability of different screen sizes for controlling the output size, the presence of safety features, ease of maintenance, energy efficiency, automation options, monitoring options, availability of industrial air pollution control system, etc.
- Consult with Manufacturers or Suppliers:
It is very important to consult with shredder manufacturers or suppliers who have expertise in metal shredding. They can provide real insight into the right type of shredder for your specific needs, based on factors such as your material requirements, production volume, and budget.
- Evaluate Cost and ROI:
Consider the cost of the shredder, including the initial purchase price, installation costs, and ongoing operating costs such as maintenance, energy consumption, and spare parts. Evaluate the return on investment (ROI) based on the expected benefits of the shredder in terms of increased productivity, reduced downtime, improved material handling, and other relevant factors.
By considering your shredding requirements, input material characteristics, shredder types, feedback from consulting with experts, and evaluating costs and ROI, you can select the right type of shredder that best meets your needs and ensures efficient and effective metal shredding operations